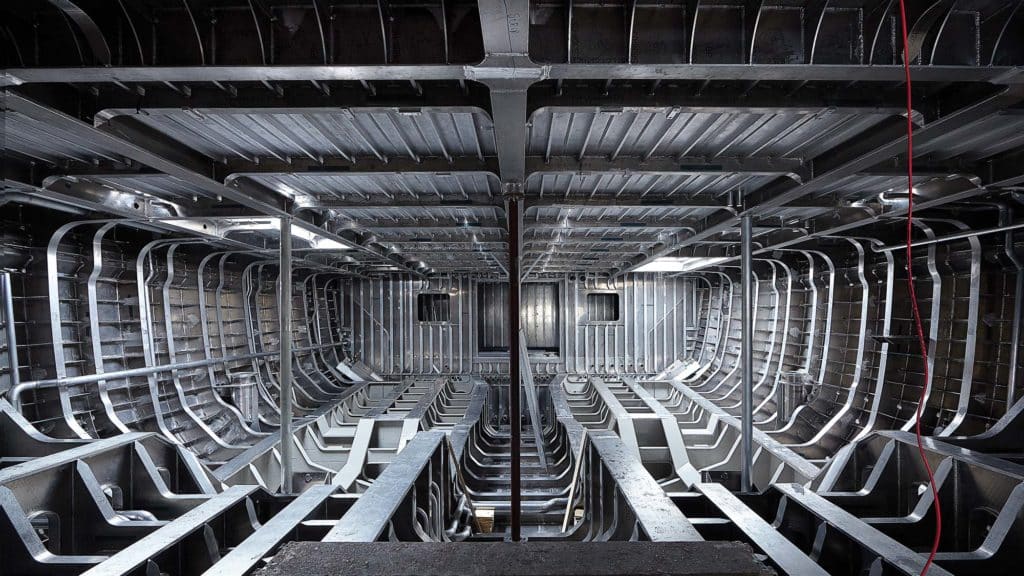
This past summer, a handful of cranes lifted the massive aluminum superstructure for Project Cosmos into the air at Heesen Yachts, in preparation for joining the superstructure with the aluminum hull. The 1,700-gross-ton 262-footer is the largest yacht by volume and length in the Dutch shipyard’s history.
As exciting as the moment was for those reasons, it was arguably more exciting for the builder’s team because of Project Cosmos’ challenging construction and engineering. Incorporating a shipyard-patented hull component, the yacht is poised to cruise upward of 20 knots and top out at 30 knots.
The excitement in the air may have been reminiscent of a similar scene in 1979, when the 66-foot <i>Amigo</i> launched. <i>Amigo</i> was by far the largest yacht that a Dutch entrepreneur, Frans Heesen, had built. It was also the first yacht under his then-fledgling brand, Heesen Yachts.
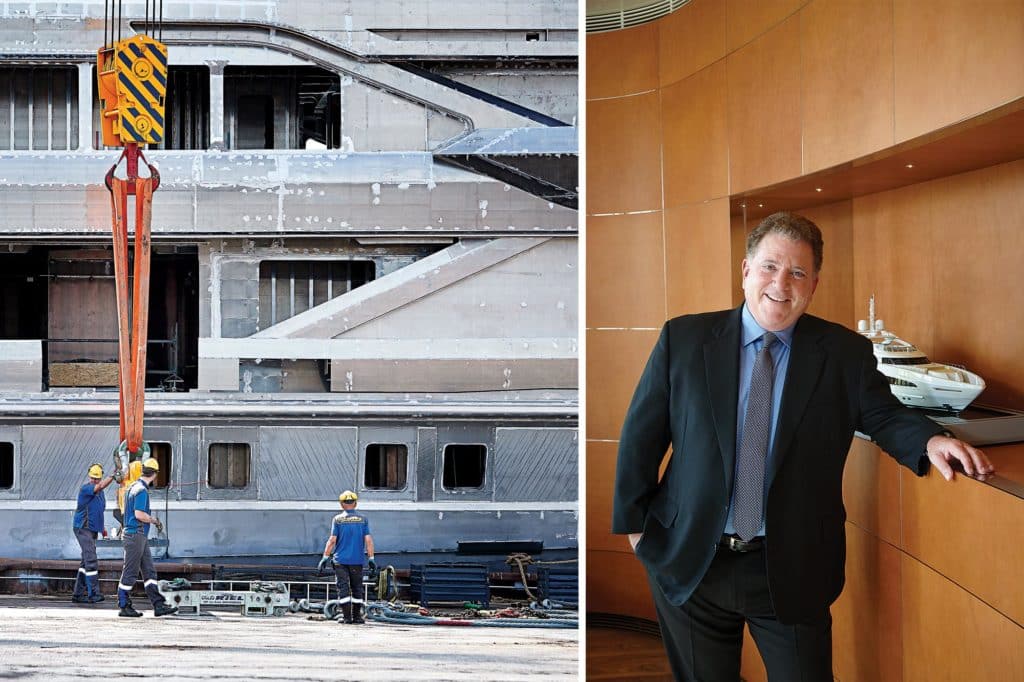
With a business background in plastics, he had acquired the Striker Boats shipyard in 1978, initially for other purposes but ultimately deciding to keep boatbuilding operations going. He prioritized constructing aluminum yachts and marrying performance with luxury. In the ensuing years, Heesen Yachts earned a global reputation for both sport-fishing and performance designs.
While Frans Heesen sold the yard in 2008 and retired in 2012, the company hasn’t retreated from its pioneering path. During the past decade, it has delivered about two dozen aluminum yachts between 121 and 230 feet, as well as 18 steel-hulled yachts up to 184 feet length overall. While most have been semicustom and started on spec, Heesen replaces models regularly and is increasingly pursuing fully custom projects.
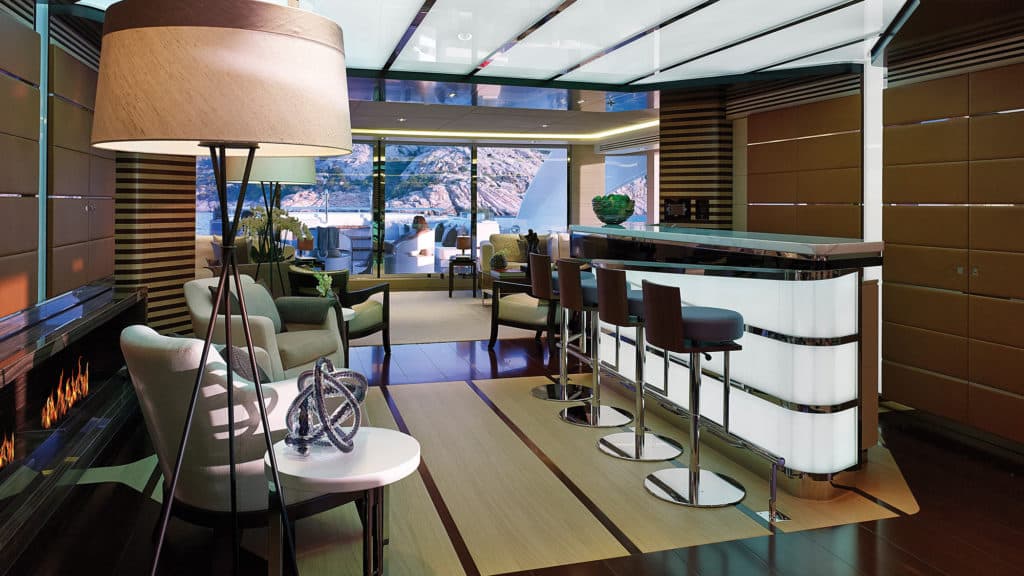
The builder can work on as many as eight yachts annually and is aiming for a larger share of the supersize-yacht market, with a 279-foot-long dry dock within a 295-foot-long construction shed. And Heesen Interiors recently added 24,000 square feet to its headquarters. The site now encompasses nearly 87,200 square feet. Staffed with draftsmen, cabinetmakers, wood finishers, upholsterers and more, Heesen Interiors is among the few full-service interiors departments under a superyacht shipyard’s ownership.
“It’s a constant evolution at the shipyard to try to stay current—because technology changes,” says Thom Conboy, US director of sales. Building on spec can run the risk of doing things the same way again and again, “but to try to continue to be on the cutting edge with spec boats is a fine balance between innovation and profit.”
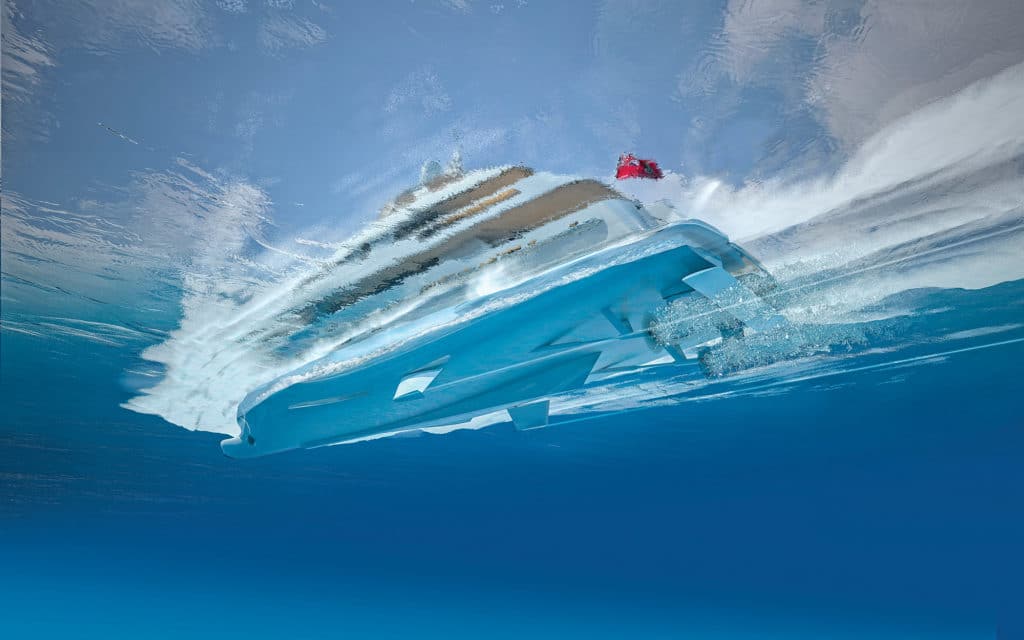
A good example of striving for innovation is Heesen’s use of the fast-displacement hull form. Designed by Van Oossanen Naval Architects, it reduces hydrodynamic resistance throughout a yacht’s full speed range and reduces fuel consumption by about 15 to 20 percent. Heesen became the first builder to adopt it with the 213-foot <i>Galactica Star</i> in 2013. The hull form is now standard on several of Heesen’s series models in aluminum and steel.
The shipyard also adopted technical advances such as the Hull Vane, another Van Oossanen creation. Like a spoiler on a car, the Hull Vane is a foil, or a wing, that helps to create thrust while reducing drag, pitching and fuel consumption. The steel-hulled <i>Alive</i>, a 139-footer started on spec and delivered in 2014, was the first yacht to use the Hull Vane.
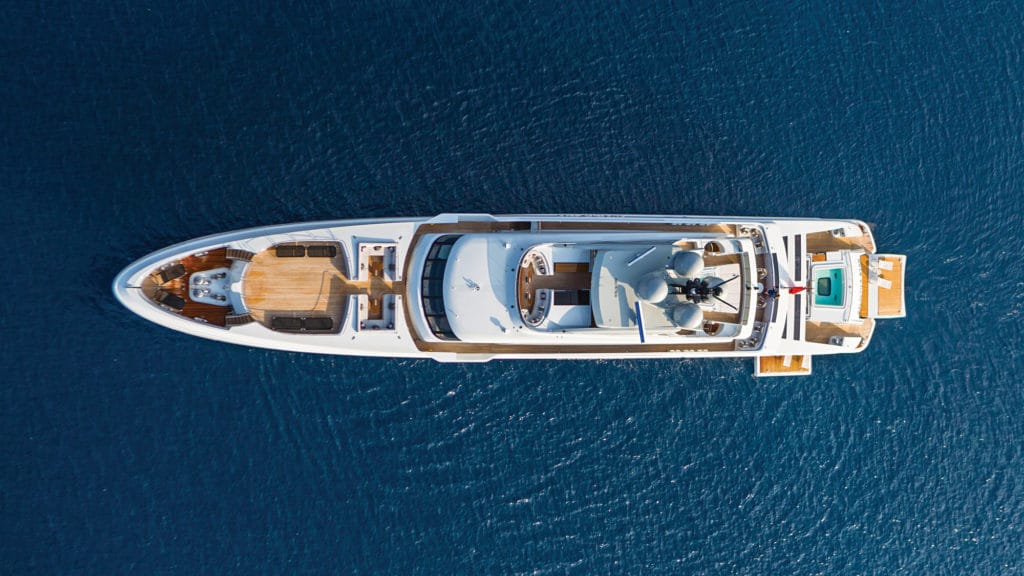
“With these spec boats, we’re not one of those shipyards that set out to build a run of 20, 30, 40 sisterships,” says Mark Cavendish, Heesen’s director of sales and marketing. Heesen limits each series to about 10 to 12 yachts, sometimes even fewer. “Then we’ll stop and redesign and engineer a whole new model. We’re not just taking the hull and tweaking it slightly; we’ll actually tear up the blueprints and settle down and look at what the latest technology can offer owners.”
Then, the Heesen team adds in owners’ ideas. “We’re known to be a flexible yard,” Conboy says. “If it makes sense and helps the sale, we’ll look at it.”
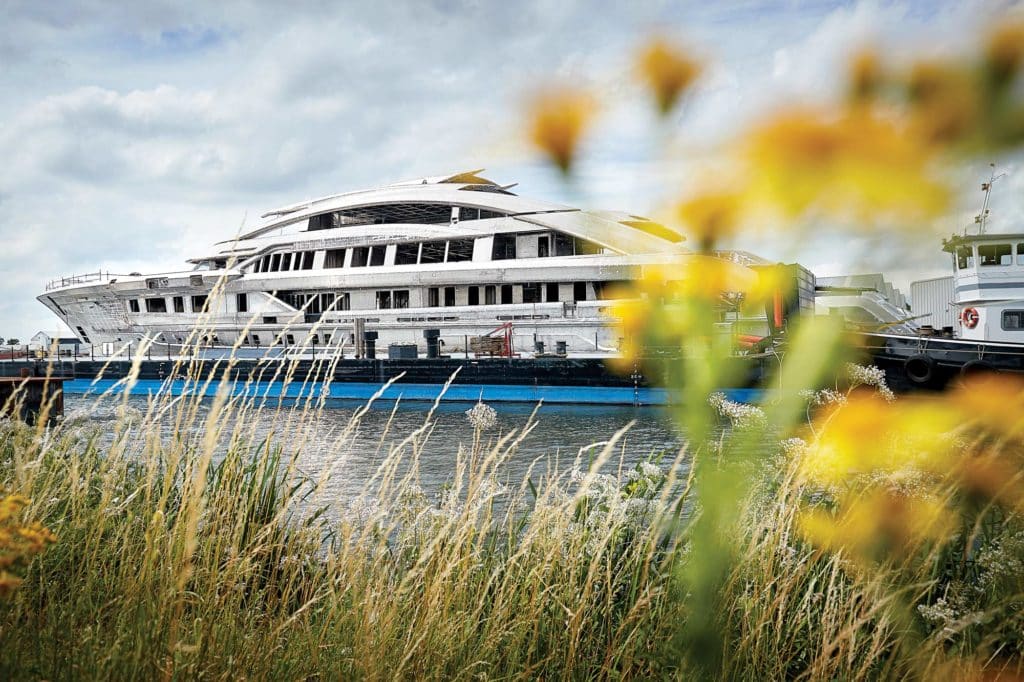
Even with its history of series builds, Heesen is fielding requests for fully custom yachts. Two notable contracts are Project Skyfall and the above-mentioned Project Cosmos. The latter’s quadruple MTU engines totaling 19,000-plus horsepower are expected to deliver a punch that requires rigidity and light weight in the yacht’s construction. Heesen’s in-house solution is a patented structure called the Backbone. Similar to an I-beam, the top of the Backbone runs port to starboard on deck, while the bottom forms the keel. The yacht’s hull spans the middle. Upon delivery in 2022, Project Cosmos should be the fastest all-aluminum yacht of its size.
That’s more than “something fresh in the offing,” as Cavendish describes Heesen’s operations. It’s bound to be a stiff breeze blowing customers’ hair straight out.
Take the next step: heesenyachts.com