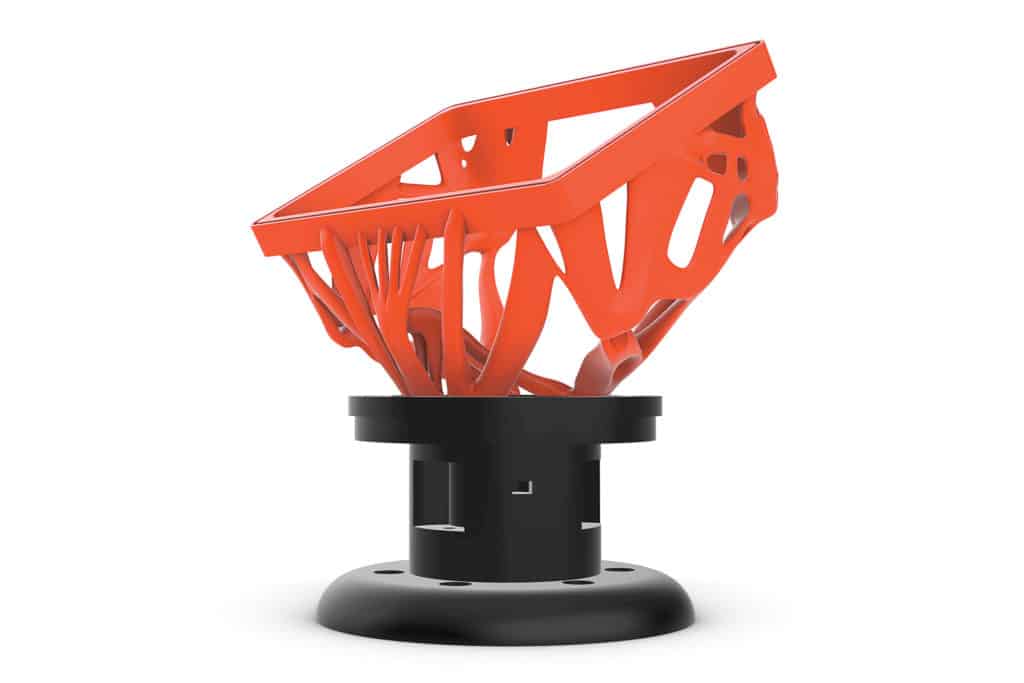
Last fall, when the University of Maine announced that it had created the world’s largest 3D-printed boat, imaginations ran wild. The idea of pressing a touchscreen and having a boat spit out of a gigantic printer suddenly felt possible. The notion of having a boat designed in a newfangled shape became a realistic-sounding option. And because the team in Maine had printed the 25-foot boat in just 72 hours, dreams of having production boats fly off factory lines became the stuff of serious conversations.
Practically speaking, here in reality, things are moving a bit slower on the innovation timeline. Habib Joseph Dagher, who leads the project as director of the university’s Advanced Structures and Composites Center, says the most likely immediate outcome will be a new way to make boat molds in the 50-foot range. “We think some of the first products that will come out over the next year will be full-size or close-to-full-size molds for boats made of recyclable materials,” Dagher says. “We think what’s going to happen next is shipyards evaluating the molds and giving us feedback, so we can get the technology honed in and able to roll out on a commercial scale.”
It’s a baby step in what experts say will be leaps and bounds of creative uses for 3D-printing technology once it can be harnessed to its full potential. Additive manufacturing, as it’s also known, is now the stuff of tests and experiments in fields as wide-ranging as aerospace and dentistry. Researchers are figuring out all kinds of materials that can be 3D-printed, as well as all kinds of ways to build the 3D printers themselves. The US Army is testing ways to use the machines in fields of combat, to print replacement parts on demand. Carnegie Mellon University just got funding to create software that will identify components in a CAD file that can be optimized and built better, such as in a different shape to reduce weight. BMW recently opened an entire additive-manufacturing campus in Germany, looking to improve upon the 300,000 or so parts the company built this way in 2019.
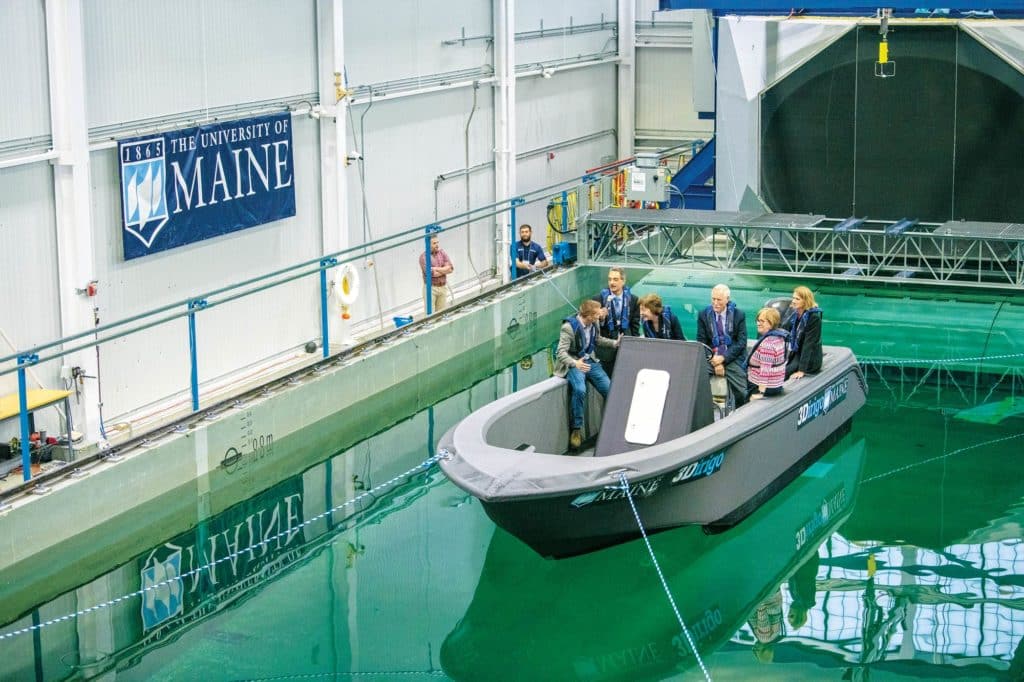
“One day, we’ll all be printing boats without a mold,” Dagher says, “but we’re all going to have to wait a little bit for that.”
As far as boats go, advances are happening all around the world. At the IYRS School of Technology and Trades in Rhode Island, the Digital Modeling and Fabrication Program is heading into its fourth year. Jeff Elsbecker, who heads it up, says that to understand where 3D-printing technology is today, we have to think about printers from the 1980s.
“If you remember dot-matrix printers, I would say that 3D-printing technology is almost where dot-matrix printers were,” Elsbecker says. “We’ll follow that with lasers and jet printing and all kinds of things. I suppose the far end would be replicators like in Star Trek.”
IYRS is focusing on teaching students design fundamentals and the basics of the technology. By the time they start working in naval-architecture firms or shipyards a few years from now, everything will have changed many times over, but the fundamental skills will still be needed to use whatever form the technology takes.
“There’s so many people doing so many things, one of the issues is also getting the machines to communicate with each other,” he says. “It’s sort of like deciding whether to go with beta or VHF. It’s at that stage.”
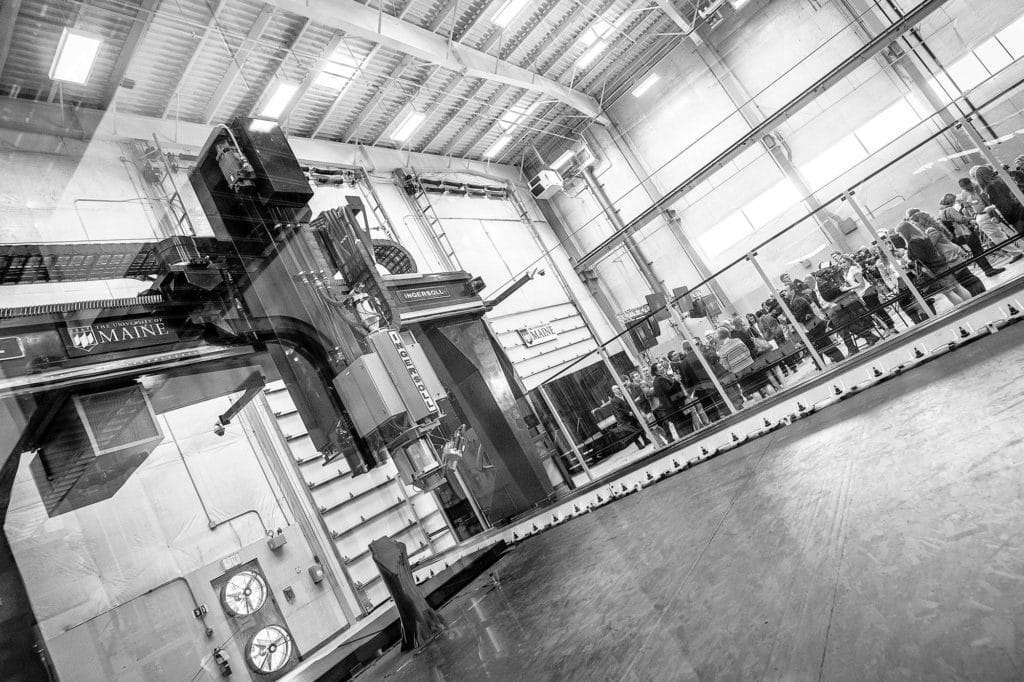
Boatbuilders who are early adopters in the 3D-printing world are using the technology for things like components and molds, says Bill Kenyon, director of education at IYRS. One example, he says, is Brooklin Boat Yard in Maine. It’s mostly a traditional boatbuilding and repair facility.
“When I was up there in January, they showed us a bow chock that the guys had designed,” Kenyon says. “They worked it all up in CAD and sent it off to a company that 3D-printed a prototype. They got it back, tweaked their design, sent it a couple of times, and then the guy could print it for them in titanium.”
Similar experimentation is happening in Auckland, New Zealand, where Richard Booten, head of design at Yachting Developments, says the yard’s purchase of 3D printers led to all kinds of ideas.
“Once you’ve got the machines, you start thinking about what you can use them for,” Booten says. “A lot of what we use them for is printing hull components—anything that has a highly complex shape. We’ve done exhaust-tube fittings. We’ve done hull fittings. We’ve achieved all sorts of stuff. Anything we would traditionally have gone and built on a CNC at great expense, we have done that. It’s really saving us some money by doing that.”
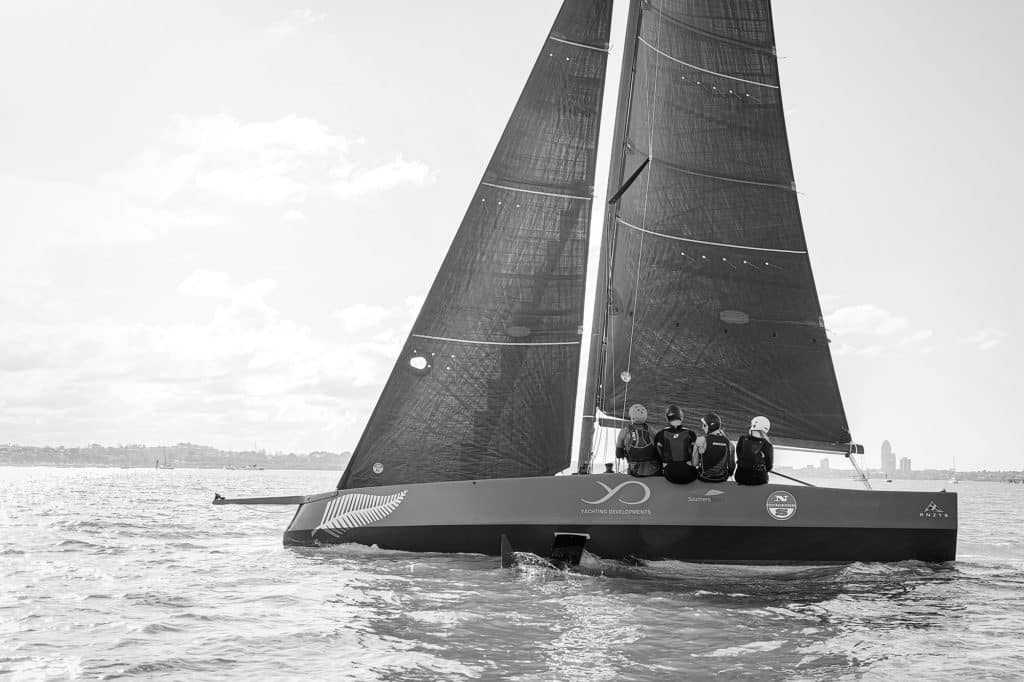
Yachting Developments is also now using the technology to plan vessel refits, to help clients understand how a final component will look and feel.
“The boat in the shed at the moment that we’re doing a refit to, they’re putting a new screen on the helm console,” Booten says. “Before we committed to making something out of carbon or fiberglass, we are able to print that addition and melt the screen in it so the captain can see what he’s actually going to get in real life. I think we’ve printed two or three of them now, and he’s changed stuff along the way. It’s relatively inexpensive to do that. Before, you’d kind of do it on the computer screen, and everybody would peer at it. The real-life version can look a bit different, so this is a real advantage.”
What will come next for the technology in boatbuilding, he says, is anybody’s guess. Right now, 3D-printing materials don’t compare to
fiberglass or carbon in terms of strength for building hulls, but new materials are being developed all the time. Most boatbuilders can’t afford a mammoth-scale 3D printer of their own, so they’re limited by whatever additive-manufacturing company can do the printing off-site. Boatbuilders, like everyone else, are just trying to keep up with the technology and think toward the future.
“There’s people around the world playing with all sorts of stuff with regard to 3D printing,” Booten says. “There’s people printing houses. There’s people printing bridges with welders stuck on the end of robots. It’s only going to gain more traction as a process and in the industry over the coming years.”
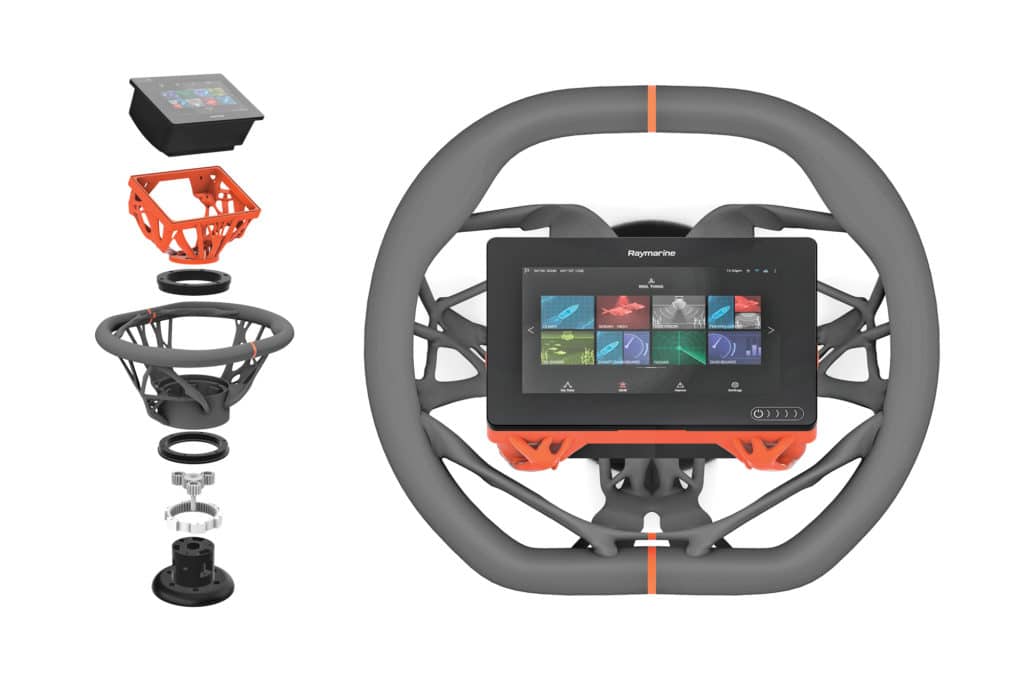
Old and New
It’s an odd thing, hearing the name Nathanael Herreshoff mentioned in the same sentence as 3D printing.
Herreshoff, of course, is the yacht designer best known for his America’s Cup designs of the late 1800s and early 1900s. He died in 1938, a time when the V-8 engine and the metal-cutting contour band saw were bleeding-edge technology.
The 3D printer wasn’t invented until decades later, in the 1980s. But that’s not stopping the team at the IYRS School of Technology and Trades in Newport, Rhode Island, from using the modern tech to build a Herreshoff.
This past year, the team was creating a replica of a 100-year-old Herreshoff design. Some of the hardware that Herreshoff had specified on the plans was not to standard; it had to be custom-made. IYRS decided to make it with 3D printing, converting the original drawings into files the printer could read.
“They worked them up in CAD and printed a 3D pattern, and the pieces could be made out of bronze,” Bill Kenyon, director of education, says of the team that Jeff Elsbecker leads at the school.
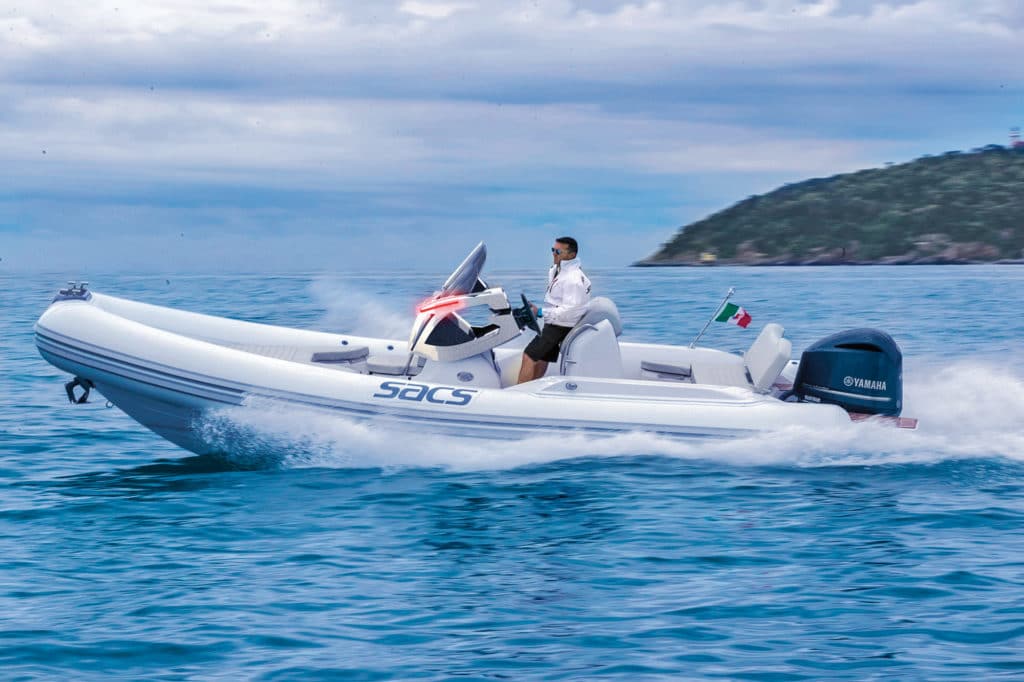
Scaling Up
Superfici, a company based in the superyacht-building mecca of La Spezia, Italy, is using 3D printing in myriad ways, such as to create the sailboat rigging shown above. Paolo Licinio Nazzaro, at right in the photo below, is the company’s co-founder and managing director. His team worked with the owner of an Amer 94 to create what they say is the first 3D-printed helm console. It looked just like a traditional console, made from regular design plans.
Next, Superfici worked with Sacs to design and 3D-print the helm console shown on the opposite page. This console is a shape that can’t be created with a traditional mold, and the multifunction display is integrated in a way that lets it be upgraded later.
Today, the company is thinking about ways to make entirely new boat hulls, with features such as integrated lights and fenders.