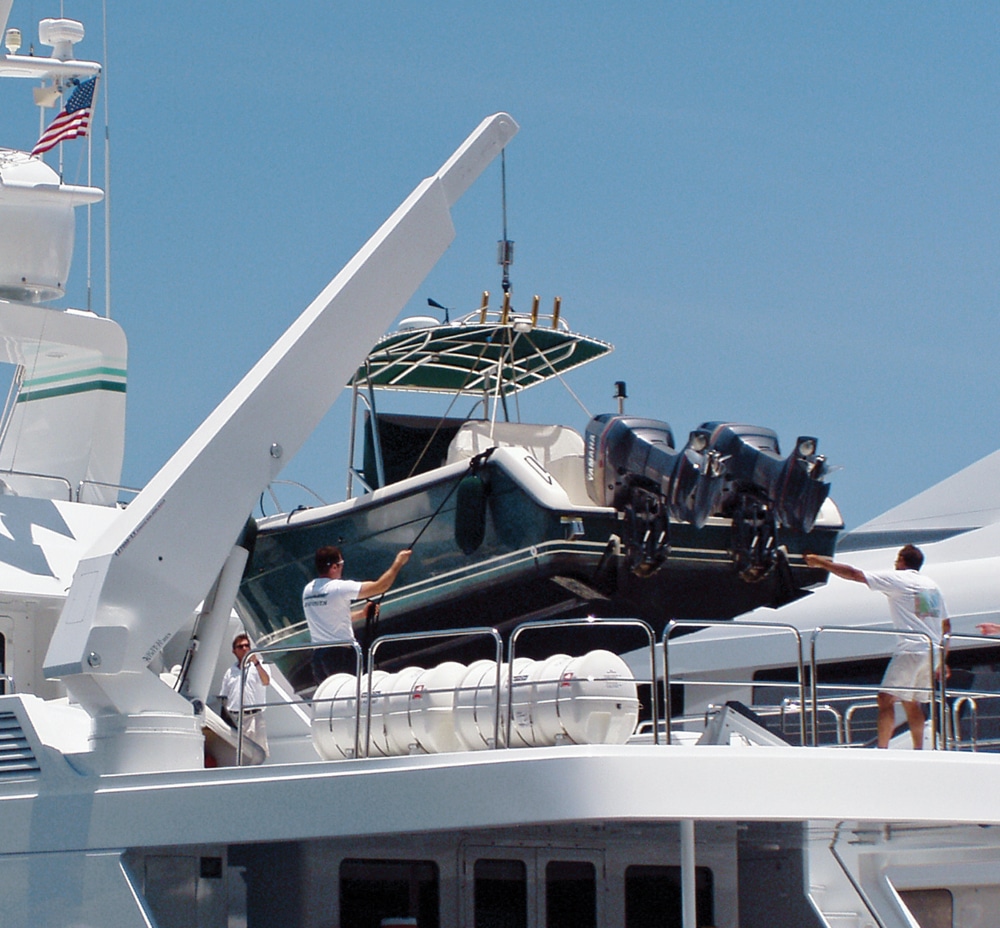
Davit Maintenance
Today’s davits are compact, low-profile structures painted to match their surroundings and often even integrated into the boat, barely noticeable when idle. It’s easy to take them for granted until considering their loads. A 1,000-pound tender at the end of a 10-foot davit boom places 10,000 foot-pounds of force on the davit’s base. Linear winches, which employ a hydraulic ram to expand or contract what is typically a six-part block and tackle, require six pounds of force plus friction losses for every pound lifted — 7,000 pounds or more working on internal components for that same half-ton small boat. Given the consequences of a failure, proper davit maintenance is paramount.
The first tool to employ for davit maintenance is a freshwater hose. “The workings are housed inside the davit and hidden with a pretty fiberglass cover, where you don’t see corrosion that’s starting,” says Rick Thomas, vice president of Nautical Structures Industries (www.nautical-structures.com). “Blow fresh water down inside that boom. That gets salt crystals out of the cable and pulleys.” An occasional spray of corrosion inhibitor like Boeshield T-9 also avoids many problems, and prompt attention to minor corrosion nips major deterioration in the bud. “Many internal parts are steel,” Thomas says. “A wire brush and a can of Rust-Oleum go a long way. What could have been a small repair bill often becomes a major project. It doesn’t have to be that way.” Cables are probably the biggest source of trouble — and among the most serious. Salt works down into crimped fittings and causes corrosion where it can’t be seen. On vessels maintaining class certification, cables are replaced every other year and reversed, end for end, in between.
“It’s cheap insurance,” Thomas says. Kinked or pinched cables are problems that can be prevented with proper cable handling. Maintain constant pressure with a rope when raising an unloaded cable, and store the davit with the cable under load for continued smooth operation. Nautical Structures sets its davits so the weighted “headache ball” pulls against the end of the davit at the limit of its travel with about 1,000 pounds of pressure on the cable. Winch davits aren’t as automated. “Pull up until the ball touches and then retract the cable until you hear it pull tight,” Thomas says. Newer hydraulic davits with linear winches are much more forgiving than older electric-winch davits. Once winch drums start looking like birds’ nests, problems carry to all components, because the cable will often suddenly jump while lowering a tender. “A two- or three-inch drop doesn’t sound like much, but that puts a tremendous shock load on the system,” Thomas says.
Spectra and other high-tech composites are sometimes used in place of steel. The material generally doesn’t develop sharp snags as stainless steel cables do, but periodic inspection is critical. “Spectra has over three times the strength of steel wire, but only when it is intact,” Thomas says. Sun breaks down Spectra, so the material should always be stored completely inside the davit. Address any signs of chafe coming from inside the davit immediately. Stainless wire is more forgiving, but when internal components aren’t working smoothly, loads increase dramatically. “Relax the cable and look in and inspect everything. You should be able to spin those pulleys freely, and they shouldn’t wobble,” Thomas says. Even with regular checks, he says, davits should be serviced every two to three years.
Simple electric winch davits have largely given way to hydraulic davits with power rotation, boom elevation and even boom extension, which add safety and flexibility. Hydraulic systems cause few problems, as long as the oil is clean. Thomas likes to see more than just a filter where low pressure fluid returns to the pump, but also, less common and more important, a three- to five-micron high-pressure filter in line just after the pump, which he says heads off many problems with sensitive hydraulic valves. Both filters should be changed every year or two. Do a complete oil change using only the recommended oil every three to four years.
Maintenance doesn’t end at the davit hook either. “Inspect the lifting harness and [the tender’s] lifting points often,” says Brian Bohne, manager of Inflatable Services and 84 Boat Works in Fort Lauderdale, Florida (www.84boatworks.com). He’s seen a half-dozen failures in that area in his 30 years there. Salt penetrates cables inside Nicopress fittings where corrosion can’t be seen, particularly on lifting bridles made with heavy heat-shrink tubing covering those fittings. “We used to heat-shrink them,” Bohne says, since the rubber coating looks better and protects the tender from scratches. “But you can’t inspect them.” Bohne also makes bridles with 1/4-inch cable and hardware all rated to 5,000 pounds for each leg. Spectra lifting bridles are handy to stow and easier on gelcoat surfaces, but Bohne worries about bridles left in the sun. “When do you know it’s time to replace it?” he asks. He also prefers stainless-steel cable tender tie-downs instead of ratcheting straps for the same reason.
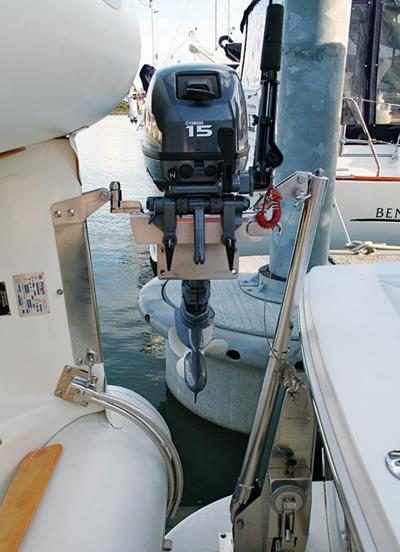
Davits are worth conscientious, careful maintenance because tenders provide such freedom, and having them aboard is great peace of mind. Owners of smaller yachts may get tired of towing the tender but don’t have the deck space to secure one. That’s where Weaver Marine Products’ hoist lever system (www.weaverindustries.com) comes in: It’s a dinghy-lifting mechanism, bridle, chocks and tie-downs combined. Pads are mounted to an inflatable’s rigid hull and transom and also on the swim platform, with stainless brackets between the two forming a pair of hinges. Some models use a small electric davit mounted on the swim step to raise the tender, hinged on its port or starboard beam end, while a proprietary outboard mount on the tender pivots with the davit arm, automatically stowing the outboard vertically about 15 inches away from the tender. While it’s only suitable for boat and motor combinations up to 400 pounds — typically a small rigid-hulled inflatable with a 15- or 20-horse outboard — Weaver’s outboard bracket accommodates electrical wires as well as steering and shift cables.
“The systems are pretty much maintenance-free,” says Jason Fetting, Weaver’s sales manager. “Use soap and water to keep the salt off and polish to clean up any rust.” Like davits and chocks, the Weaver system needs periodic inspection where hardware attaches to the boat and the tender. Hydraulic systems are quite simple — just watch for the dirt accumulation that might indicate an oil leak, as well as corrosion that shows seawater is finding its way onto the unit. Fetting says the provided locking pins should always be used to secure the hinge fittings and to hold the davit in its raised position.
Davits and lifting hardware can stand up and be reliable in the marine environment when they get the maintenance they need. But lifting a heavy dinghy high in the air is one of the most dangerous jobs on board. Take care of that hardware and treat it with respect.
Tend to Your Tender
Here are trouble spots to avoid and simple solutions to try.
Brian Bohne, manager of Inflatable Services and 84 Boat Works in Fort Lauderdale, warns never to lift tenders while the yacht is on the hard — the leverage created by a load high and to one side isn’t anticipated when boats are blocked. He also advises against towing jet boats. “It forces water into the engine,” Bohne says. “That’s a $15,000 mistake.”
Ethanol-blended gasoline is also causing expensive engine repairs. “I’ve literally seen gas go bad in 30 days,” he says, owing to ethanol’s ability to absorb moisture. “Carburetors weren’t tolerant of fuel problems. Fuel injection solved that, but now ethanol is changing things.” Bohne recommends using Nexus Ethanol Defense fuel treatment and paying careful attention to tank penetrations that could leak water in. For trouble-free tenders, he also recommends changing engine cooling impellers every year, replacing batteries every two years and installing a trickle charger.
Covering tenders while wet causes problems. “[In the hot sun] it’s like a steam bath. It turns the electrical system green,” Bohne says. It’s also hard on inflatable fabric. “Mold gets into the weave of the fabric. That won’t clean off,” he says. Bohne suggests periodically adding just a bit of bleach to wash water to kill mold spores before they develop. He also recommends Formula 88 degreaser and 303 fabric protector, and specifically warns against using ammonia or Armor All.
Inspect fabric joints on inflatables often. “Glue problems typically show up [when a boat’s age reaches] around four to six years,” Bohne says. “Deflate the tubes and check adhesives [at joints] between rubber and fiberglass, and at the attachments at the transom.” Valves should be kept covered to protect rubber seals from the sun, given a bit of silicone lube once in a while and replaced when leaky.