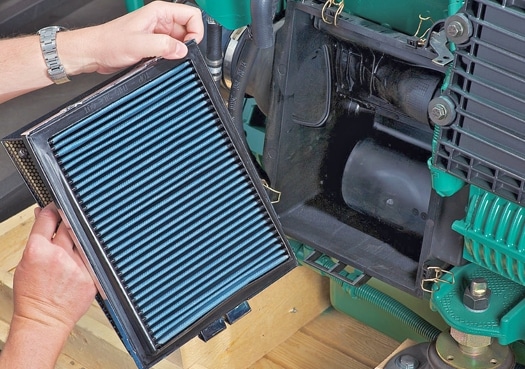
ytgoct23yy525.jpg
Your yacht’s engineroom is pristine. The engines are Awlgripped, or maybe even chromed out, if you’re that type of person. Blue silicone hoses remain perfectly unpainted; their stainless steel clamps precisely aligned-or not. However, what matters most, particularly with newer diesels that squeeze more horsepower from each drop of fuel with tighter tolerances and higher pressures, is how clean your engines are on the inside. Fuel, oil, and air filters keep them that way.
But even smart yacht owners probably don’t always think about all the danger lurking outside those filter elements. After all, the diesel fuel purchased at your marina is clean, right? Wrong, even in the best of circumstances. The refining of crude oil into its components is a tradeoff, just like any manufacturing process: It could be cleaner, but it would cost more. Diesel contains everything from ash (the industry term for various metals and inorganic contaminants) to organic compounds like toluene and xylene.
The strangest part? Engine fuel systems can handle these leftovers but they clog fuel filters, making them less effective at straining the dirt, rust, water, and other contaminants fuel picks up from the various pipes, tanks, and trucks that carry it from refinery to yacht. “Diesel fuel contains asphaltenes-that’s part of the refining process,” says Steve Hardison, fuel products manager for the Racor division of Parker Hannifin Corporation (www.parker.com/racor). “They’re going to be there until you [refine the crude oil] all the way down to kerosene. But those asphaltenes are what clog fuel filters.”
As filters become restricted, they become less effective at filtering out particulates and water that can destroy engine fuel systems. “Eighty percent of the filtration happens on the surface of that filter media,” Hardison says. “Water is supposed to be stopped on the outside of the filter, settle, and collect in the bowl [at the bottom of the filter assembly].” But clogged filters increase vacuum pressure and therefore the velocity of the fuel moving through remaining, smaller pores-think of water shooting through a small gardenhose nozzle versus an unrestricted hose. “If you wait until that filter is really plugged, now the water can go through. You can probably go [longer] before you starve the engine [of fuel], but you’ve already lost water-removal capability.”
Hardison recommends installing vacuum gauges to measure each filter’s restriction, and checking them while underway at cruise rpm to ensure filters are still doing their intended job. Vacuum gauges can be plumbed and mounted into a panel, but, on most Racor brand filters, a simple gauge kit can replace the filter housing’s top “T-handle” in about five minutes.
Sometimes fuel contaminants grow right in place. “Algae” is the catchall term for bacteria, fungi, and yeast that find perfect conditions to thrive in the dark, airless intersection where water is trapped below fuel at the bottom of a tank. Hardison says soil bacteria are a common culprit. “It’s in the air. It’s on every dust particle. Some soil bacteria just happen to like hydrocarbon,” he says. “Their waste is acidic, basically sulfuric acid that causes corrosion.” While fuel additives with biocides kill these microbes, their carcasses become black slime that clogs filters and coats the inside of filter housings, hence the “algae” misnomer.
To control these microbes, mitigate the boundary layer that they grow in by keeping fuel tanks full so they can’t collect condensation from the air, and purchasing fuel from reputable sources. Boats with chronic fuel problems might benefit from fuel polishing, which circulates fuel from the bottom of affected tanks through a large bank of centrifuges and filters. Onboard fuel polishers like Walker Engineering’s AlgaeSep do the same job on a smaller scale by keeping tanks clean, but they are more for maintenance and are not intended to correct a fullblown problem.
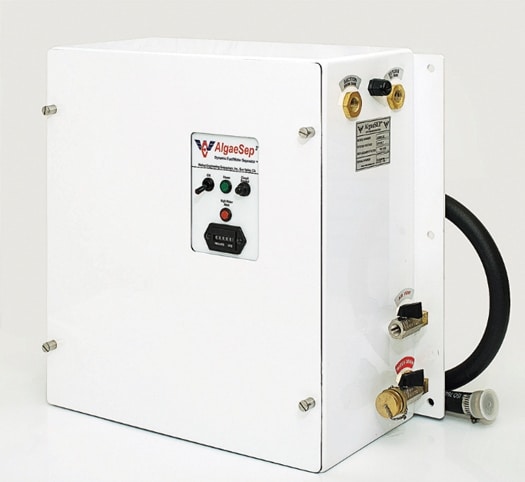
| | |
Life expectancy of fuel filter elements also depends on their porosity. On many large yachts, the primary filters- the first set in line between fuel tank and engine-only catch particles larger than 30 microns. Secondary filters, usually integral to the engine fuel system, catch smaller particles, typically down to around seven or 10 microns. In low-flow applications like generators or expedition yacht engines, primary filters can be replaced with 10- or even two-micron elements, which will clog sooner but extend the life of secondary filters.
As engine parts wear, oil picks up particles of copper, iron, and aluminum, as well as soot, dirt, and moisture from combustion air. These are collected by an engine’s oil filters, but most only strain to about 20 microns. “Particles in the four- to seven-micron range are the ones that get into the moving parts and cause wear,” says David Kline, who oversees oil-filtration products for Parker Racor. “Those wear particles and contaminants accelerate oxidation, which shortens the life of the oil’s additive package, and the oil thickens and becomes less effective at engine startup, causing metal-to-metal wear.”
One solution is bypass filtration, which diverts a small percentage of the oil away from the engine’s oil filters and into a secondary filter, where it is strained for particles as fine as three microns and returned back to the oil pan. All the engine’s oil eventually makes it through this filter, polishing the oil. Racor markets their Absolute Series Bypass Oil Filter both as a way of reducing engine wear and extending the time between oil changes, saving money in either case.
Cutting costs by purchasing off-brand oil and filters may be shortchanging your engine though, as specifications vary widely. “If a guy is spending 20 dollars on an oil filter, he’s probably getting a 20-micron filter. If he’s spending eight dollars for a filter [for the same engine], he’s probably getting a 40-micron filter,” Cline says. Quality of the materials inside the filter also varies. “They may look the same, but there is a reason one is more expensive.”
Just like fuel and oil, the air ingested by yacht engines is also filtered, although the filters vary widely. Walker Engineering has been providing high-performance air filters to engine manufacturers, as well as retrofit kits, for over two decades. “The quality of our air filtration compared to wire-cage filters is night and day,” says Michael DeLillo, head of sales and marketing at Walker Engineering (www.walkerairsep.com). “When you compare ours to a paper element, the paper can’t pass as much air so the filter has to be bigger. Our media also performs if it gets wet or is exposed to high humidity.” The tradeoff for cleaner air is that Walker’s filters have to be cleaned and then sprayed with a conditioning oil every 300 hours or so, and replaced after three or four cleanings.
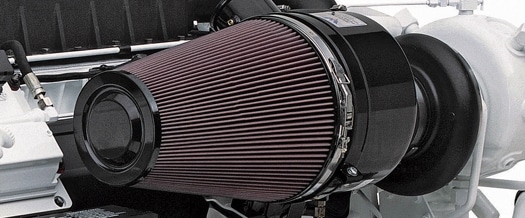
| | |
Although they manufacture standalone air filters and air silencers, Walker’s AirSep is the company’s most recognizable product. As turbo chargers and higher cylinder-compression ratios bumped horsepower ratings in the early 1980s, oily fumes from inside the engine crankcase would coat the inside of enginerooms. Developed in response, AirSeps collect and separate the oil from this crankcase vapor, draining the oil back to that pan and injecting oil-free air into the turbochargers, actually creating a vacuum inside the crankcase.
Today most new engines come with some sort of crankcase ventilation system. Many, like Racor’s setup, are available for aftermarket installation as well. Walker’s AirSep has a high-performance air filter, an air silencer to mitigate turbocharger whine, and a crankcase ventilation system, all in one package.
Walker also offers a version of the AirSep for later-model engines. “Twenty years ago the air [in the crankcase] was like tiny liquid droplets. With these newer engines, it’s almost like oily smoke,” DeLillo says, citing the tighter tolerances within engines as the main cause. “The older AirSeps were designed to eliminate oily mist, but now we’re going for oil particles as small as threetenths of a micron.” To increase the AirSeps’ performance without increasing their size, Walker simply added a disposable element inside the unit, which needs to be replaced every 400 to 500 hours.
Whether you value the look of a showroom- quality engineroom, or don’t worry about a few grease smudges and wrench marks blemishing engines that sport a quick “puff can” paint job, keep those filters-and your engines’ innards-pristine.