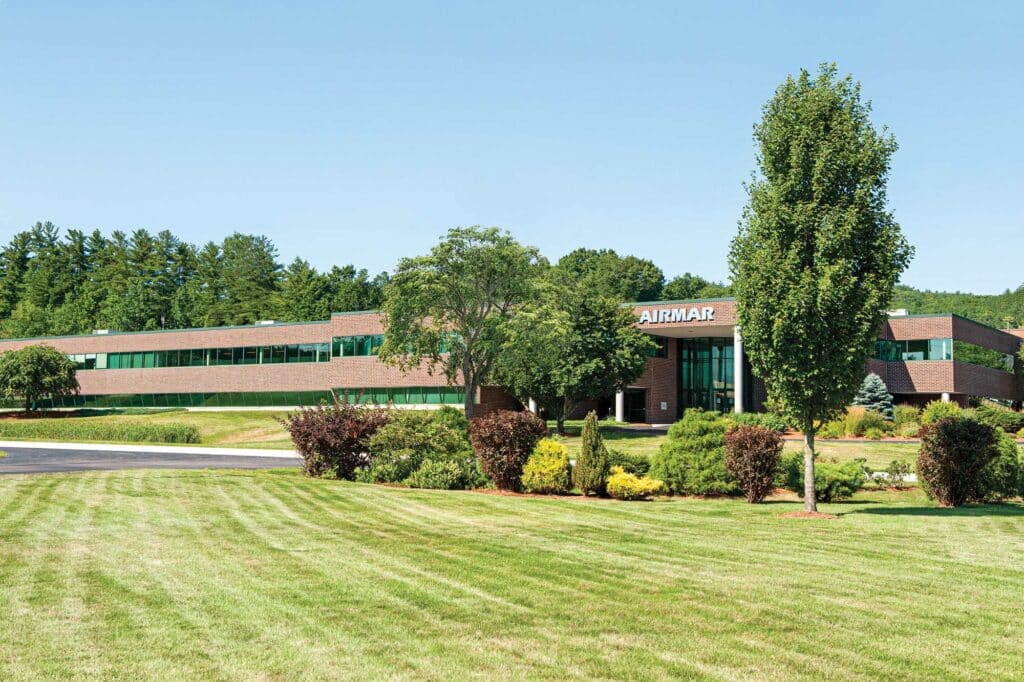
Black cables of different lengths hang from tines, awaiting testing. Each cable is fitted with connectors that align with hardware from all the marine-electronics manufacturers. If all goes well with the tests, then packaging and shipping are next.
While it’s odd to see just-minted cabling for Furuno, Garmin, Humminbird, Raymarine and Simrad on the same factory floor, that’s how this place works. Since its founding in 1982, Airmar Technology Corp. has ensured that its transducers play nicely with third-party fish finders, sonars and multifunction displays. As Craig Cushman, Airmar’s director of marketing, explains by analogy: “We don’t build marine electronics. We build high-end speakers.”
In 1982, engineer Steve Boucher founded Airmar in Milford, New Hampshire, with the goal of innovating and manufacturing better acoustic-sensing transducers. The company’s first product was a transom-mounted transducer that worked with a variety of fish finders. Today, Airmar makes everything from proximity sensors to acoustic rain sensors to flow sensors to high-end chirp transducers. The common denominator in all this product diversity is Airmar’s expertise in sonar and ultrasonic-sensing technologies. The company is the leading global manufacturer of high-end transducers.
Since its founding, Airmar has produced both branded and white-label products for third-party companies. This arrangement has freed marine-electronics manufacturers to pursue their own areas of expertise, and has let Airmar form close-knit partnerships to produce transducers that are critical to many big players’ products.
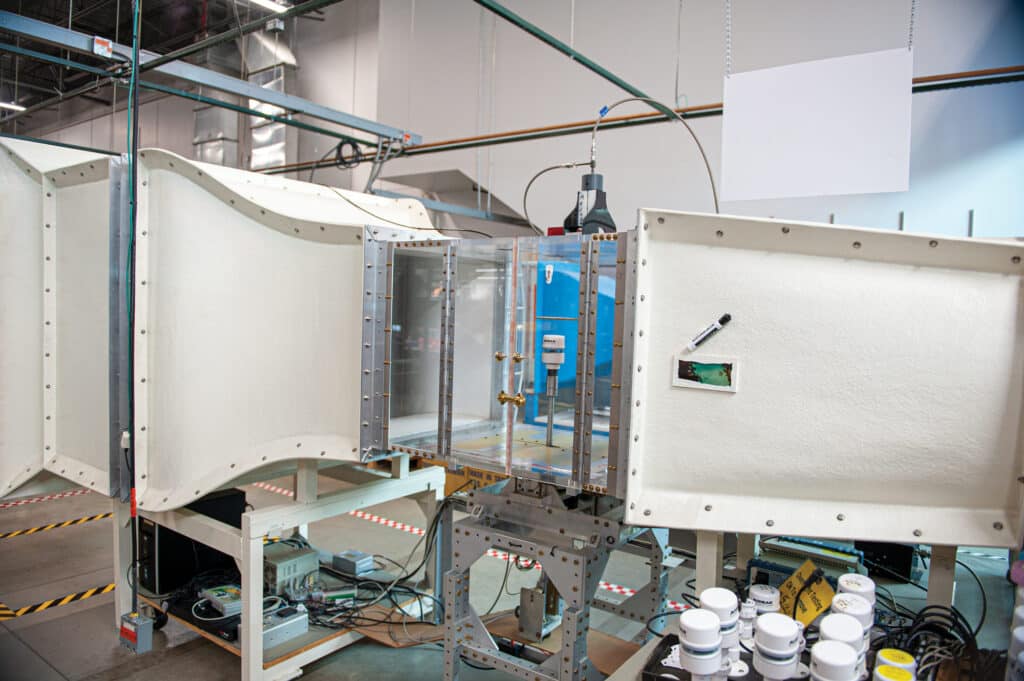
Just as Airmar grew its product portfolio from a humble, transom-hung transducer to sensors that now govern bottling plants and Chicago city buses, the business has also grown to include multiple other companies. These include Marport, which manufactures sensors, echo sounders, current profilers and sonars for the commercial-fishing market; Gemeco and Airmar EMEA, both distribution companies; and a defense-contracting operation. Roughly 60 percent of Airmar’s annual revenue flows from the recreational-marine market; the other 40 percent, including some defense contracting, provides stability in other markets. Airmar is supported by 435 global employees, including some who report to offices in France, Iceland and South Africa, while 275 to 300 employees work at (or remotely from) the company’s New Hampshire headquarters.
I visited that headquarters, which is sizable with three buildings. Cushman and Susan Leuci, Airmar’s media-relations specialist, started my tour by showing me a few pieces of Airmar-built equipment, including two small paddle wheels.
“That’s our new Gen2 paddle wheel,” Cushman says, adding that it delivers accurate speed-over-water metrics at boat speeds as skinny as 0.3 knots. “A young engineer and University of New Hampshire graduate spent three years perfecting that design.”
The wheel has a precise, asymmetrical shape, and a large surface area relative to its size. There’s little room for marine growth to accumulate compared with previous offerings.
“We made that here,” Cushman says, adding that while Airmar’s injection-molding machines can rapidly fabricate components, manufacturing here is still largely a manual process. “We’re not feeding components into a machine. It’s a manual, hands-on job. A lot of craftsmanship goes into these transducers.”
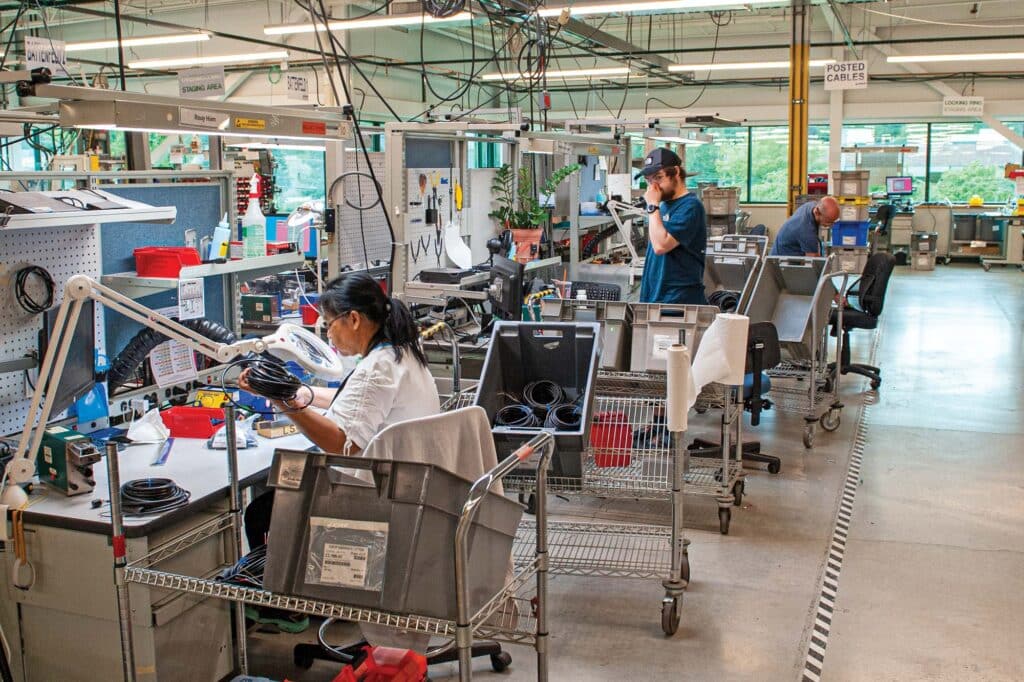
Downstairs on the factory floor, in the engineering lab, new designs are being fabricated before testing commences in the adjoining research-and-development room, which is populated with racks of testing equipment and multiple freshwater tanks. Inside one tank, a wooden structure hangs vertically in the water column. The wood is cut at different and diverging angles, which allows Airmar to test for sonar-wave reflexivity. Nearby, there’s a bench with fish finders from all the major brands. Cushman explains that Airmar tests new transducers on all platforms, just like a high-end speaker company might test its creations on receivers from all the major brands.
“We’re a technology-development company, not a boating company,” Cushman says. “We attract people because of the technology, not necessarily because it goes on a boat.”
Around the R&D room, there’s equipment for hot-and-cold cycling, drop testing and atmospheric-pressure testing. No amount of pounding into offshore seaways will approximate the level of torture that Airmar conjures here.
On the main factory floor are more tank-testing facilities and multishelf wheeled carts full of transducers ready for packaging and shipping. Their housings might be bronze, molded plastic, stainless steel or urethane, but inside, each contains at least one carefully potted piezoceramic element.
“Everything is 100 percent American-manufactured,” Cushman says. “We have some circuit boards made in Canada, but everything is assembled here, in the USA, in New Hampshire.”
Cushman leads me past the area where employees batch-test incoming componentry, before taking me into the room where other employees pour encapsulating material into transducer bodies. He says that while all Airmar employees receive months of instruction and on-the-job training, encapsulation work requires special experience to ensure that air bubbles and other contaminants don’t become suspended in the matrix.
“We have decades of research into materials that perform better in certain ways,” Cushman says, adding that a big part of Airmar’s quality comes from knowing which materials will direct the highest percentage of acoustic energy into the water column by eliminating unwanted noise.
We pass keg-like barrels filled with water and through-hull transducers, clamps and wires (and occasional rubber duckies). Rows of three-story carts hold bronze through-hull transducers, their pipe stems forming a miniature copper-colored forest.
At the ultrasonic-weather-station department, several wind tunnels occupy an end of the factory floor. They can produce winds up to 100 knots. The fans are silent as we walk by, but an engineer is preparing to test an Airmar-built weather station with an ultrasonic anemometer.
Across the street, in Airmar’s newer building, the company produces high-volume, lower-cost transducers and plastic parts, and assembles wire kits. Entire pallets of wire, wound around massive wooden spools, are ready to be cut and fitted with Airmar-built third-party connectors. “Every transducer build needs miles of cables,” Cushman says.
I couldn’t help but notice, in Cushman’s office, a half-hull of Reliance, the Nathanael Greene Herreshoff-designed behemoth that successfully defended the 1903 America’s Cup. Equipment from different marine-electronics companies is on a nearby bookshelf. Much like how Reliance dominated its field of play in its day, Airmar dominates the high-end transducer business.
The real winners, of course, are yachtsmen worldwide.
Military Service
While Airmar’s transducers detect fish, the U.S. Navy stalks submarines. MSI Transducers builds bespoke and semi-bespoke transducers for commercial and defense use. Airmar acquired MSI in 2016 and introduced high-volume manufacturing. This arrangement helps MSI be cost-competitive and gives Airmar access to next-generation technologies.