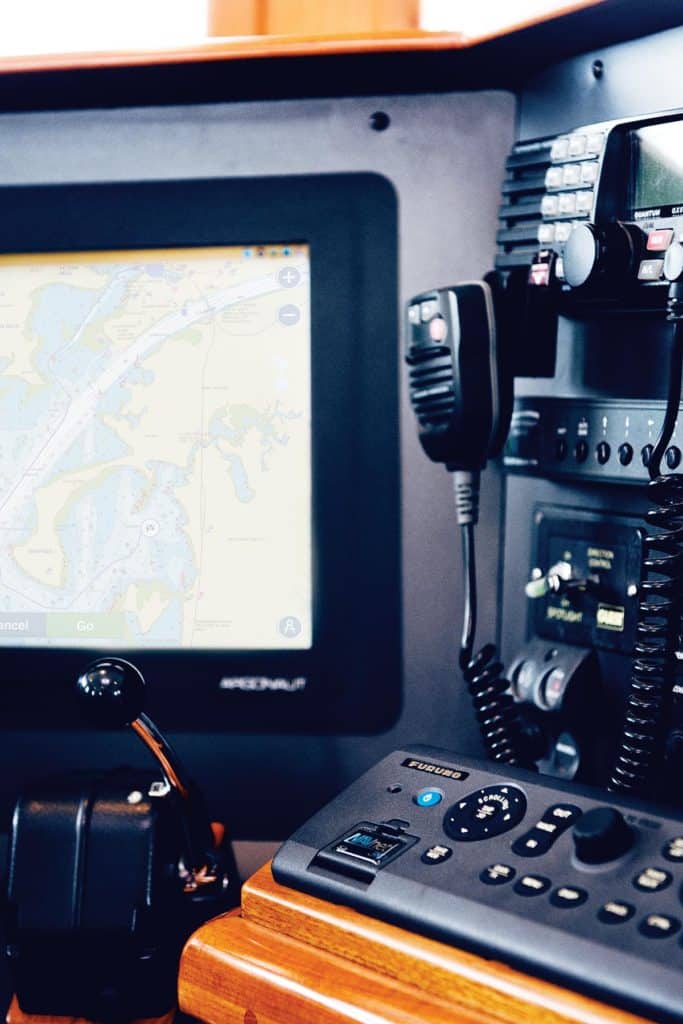
Drive the same car long enough, and its funny little noises start to blend together. Lend a friend your wheels, however, and she’ll quickly notice any mechanical shortcomings. For Dale and Joanie Dolsen of Kirkland, Washington, it wasn’t until they hired a boating instructor that they realized the aging Garmin multifunction display on their Grand Banks 46 Classic needed replacing.
“Linda showed us her iPad and the increased functionality that it offered [when paired with an MFD],” says Joanie. Based on this feedback, the Dolsens upgraded. “The new MFD is more intuitive,” says Dale. “It leads you down the path more than the old one.” In fact, the refit was so successful that the Dolsens spent a over a month confidently cruising Washington’s San Juan Islands and Canada’s Gulf Islands. While yachts can last for decades — or longer — many systems need maintenance and upgrades to sustain performance.
Engines, hydraulics and generators require regular servicing, but electronics present a different consideration; it’s far more personalized. Moreover, ever-faster processor chips, dramatically improved user interfaces and contemporary features are advancing marine electronics faster than many other onboard systems. Because of this, many pedigree vessels undergo an electronics refit every seven to 10 years.

Getting the highest return on an electronics-refit investment means selecting the right shop, having a realistic time frame and budget, and providing the necessary amount of owner input.
“A refit starts with a relationship,” says Dave Swanson, sales manager at Seattle’s Yacht Masters Northwest. “There needs to be an open line of communication and trust between owner and yard. The better the relationship, the better the project will turn out, and there will be fewer surprises.”
START SMART
The first step in any great refit is establishing open lines of communication with your shipyard. Next, it’s critical to work closely with the shop owner to spec your new equipment, and to ensure that this gear will play nicely with your existing equipment.
This relationship starts with a conversation between the shop owner and the yacht’s owner, which is the right time to discuss the project’s goals, budget and scope, as well as the shop’s experience.
“It’s important to listen carefully to what the owner wants to do with their boat,” says Larry Schildwachter, owner of Seattle’s Emerald Harbor Marine, who advised that an electronics refit could cost anywhere from $25,000 to $150,000 (or more). Schildwachter encourages owners to interview several shops about their experience working on similar yachts; their relationship with different marine-electronics manufacturers; their knowledge of the yacht’s builder; the number of technicians they will assign; and whether the same techs will be on-site every day.
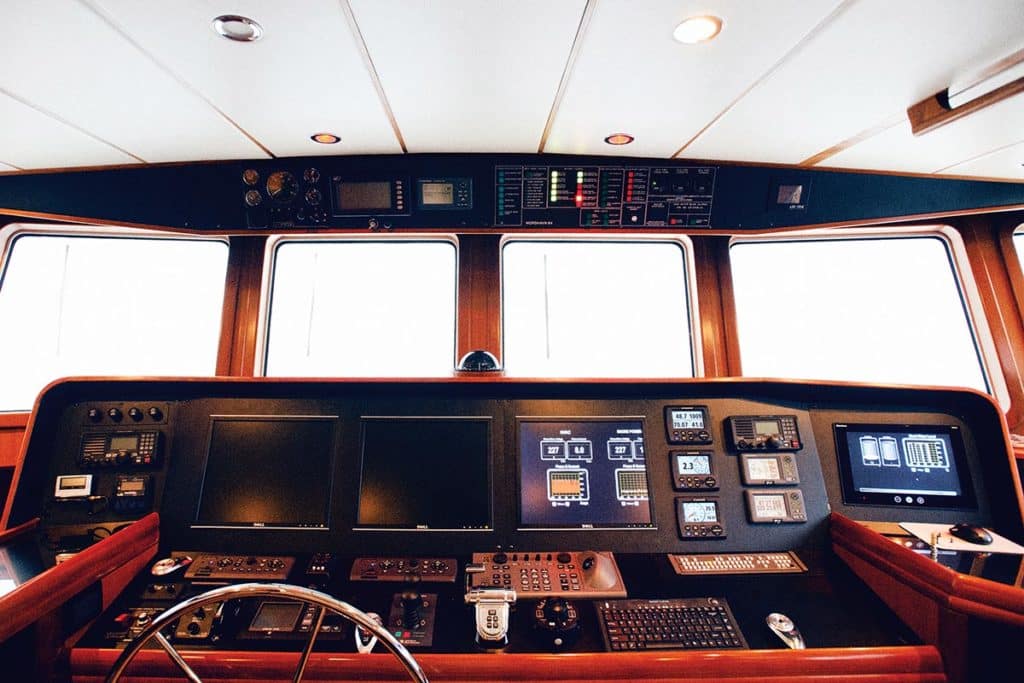
The next question is one of timing. Both Schildwachter and Swanson advise owners to start interviewing shops in September so the work can be performed during winter, when it’s least likely to interfere with cruising schedules. Fortunately, autumn is boat-show season, which presents opportunities to talk with marine-electronics manufacturers.
“Don’t be in a big hurry to spec the equipment,” Schildwachter says. “Attend boat shows and ask to sea-trial other boats with similar equipment.”
“Many pedigree vessels undergo an electronics refit every seven to 10 years.”
Swanson says an electronics refit should be “as complex as it has to be, and as simple as it can be,” so specifying the right level of technology is critical. While some owners have a detailed vision of their new helm, others need guidance. Here, a strong relationship with a marine-electronics shop can pay handsome dividends. They should be familiar with the different brands, know the local waters and know which solutions worked for other customers.
“It’s really important to ensure that the owner can use and service the gear,” says Schildwachter, who mentioned that 95 percent of his clients’ yachts are owner-operated. “It’s about determining what’s right for the owner and what’s right for the boat.”
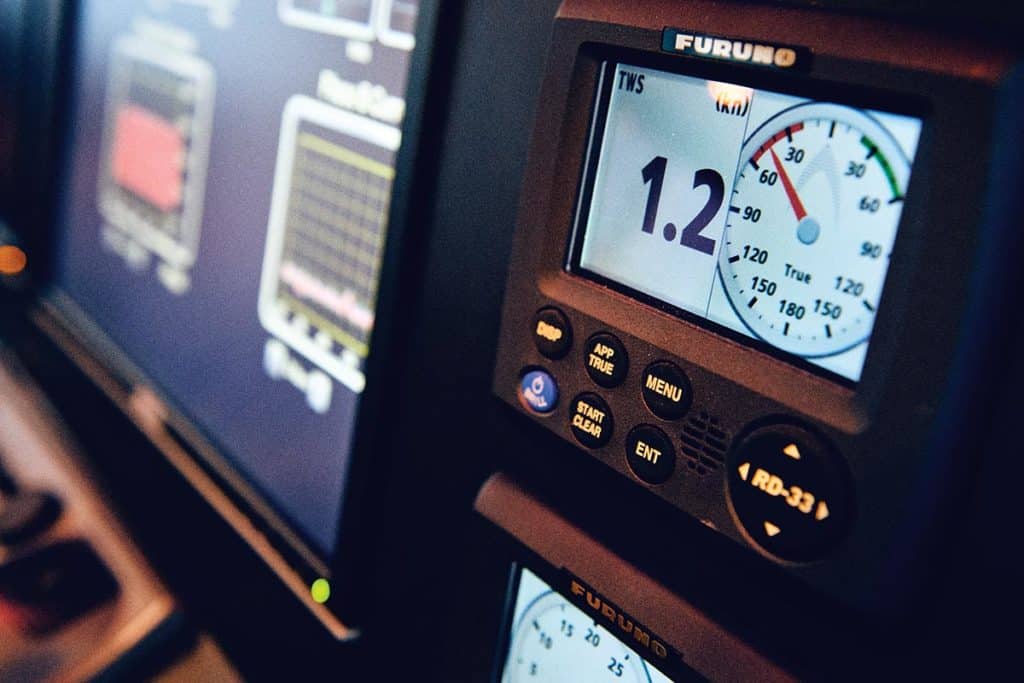
Brand-agnostic data NMEA 2000 backbones are becoming ubiquitous on new builds, but many brokerage vessels are equipped with legacy systems that require proprietary hardware (and/or software) to guarantee network compatibility. “When you get into a manufacturer’s proprietary ecosystem, you’ve got to stick with a brand,” Swanson says. Still, it’s a mistake to cling to obsolete equipment. “Generally, we replace older, outdated equipment that’s not NMEA 2000-compatable,” he adds. “Often, [integrating] newer electronics is more seamless than trying to configure older equipment.”
Schildwachter agrees, adding that while some autopilot drives can be saved, other equipment — including radar and transducer cabling and old data backbones — shouldn’t be recycled. “Our philosophy is that the gear you save could be the gear that fails or lets you down,” Schildwachter says.
THE RELATIONSHIP BEHIND THE RESULTS
John and Lin Coker weren’t planning an electronics for Hat Trick, their 2001 Little Harbor WhisperJet 38, during their first year of ownership, but that changed when they were reacquainted with Greg Allen and his team at Yacht Masters Northwest. Allen had commissioned a sailboat for the Cokers in 1979, and a relationship of trust and respect was born — two elements that John Coker identifies as critical.
“The only reason that we’ve done [our electronics refit] is because of our original handshake agreement with Greg,” Coker says. “They met or exceeded our expectations every step of the way.”
While not everyone enjoys a 37-year history with a yard, new and equally successful working relationships can be forged.
“The crew wants input,” Coker says, “and if we encourage them to give more than one perspective, [the project becomes] synergetic, and it makes for a better result.”
Once shop and owner have determined what (if any) equipment can be reused, the conversation moves to specifying equipment. This is usually handled in the form of a quote that the shop compiles and then refines in consultation with the owner. “We typically make between five and 15 quote revisions before the owner says yes,” says Schildwachter. And while change orders are usually possible, they can add time and cost, so owners are advised to consider their quote carefully before pulling the trigger. Moreover, customers should talk with their shop about the lead times involved for their purchases and plan accordingly. “We like to have 95 percent of the new gear in our hands [before] we start,” says Schildwachter.
As soon as the final quote has been accepted, a good shop will create a detailed block diagram of all onboard equipment. “Customers leave with a blueprint drawing of what their new electronics package will look like,” says Swanson. “It might not mean much to them, but when they’re stuck in Bella Bella [British Columbia], it will be super-helpful to the repair guy to see the schema.”
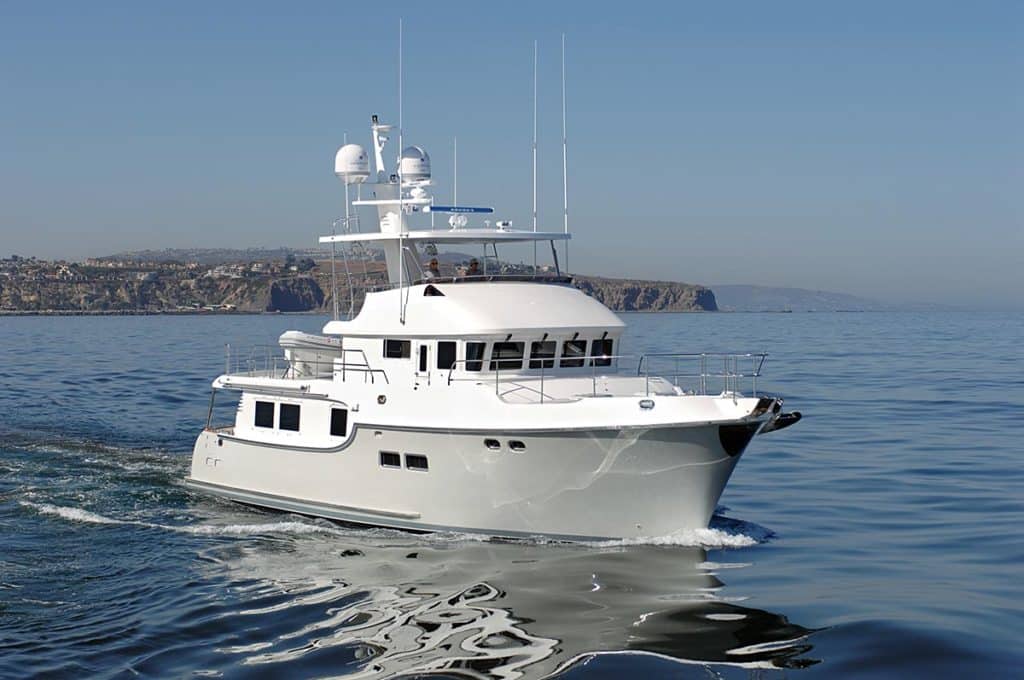
Once work begins, wise owners will stay close to the project, either via frequent yard visits (ideal) or through calls and emails. “There are a lot of decisions that [can] affect the finished price, and we want the owner to be involved in those decisions,” explains Swanson, who says that Yacht Masters Northwest keeps owners apprised of costs via biweekly invoices and regular meetings.
The final steps involve sea-trialing the new gear to verify proper performance. One good way to proceed, Schildwachter says, is for the technicians to sea-trial the equipment on their own to discover any bugs; after those issues are resolved, the shop can invite the owner for a sea trial to help familiarize him with the equipment. Schildwachter suggests that owners cruise locally for a few weekends before returning to the shop with questions, observations or requests. It could take a few post-refit visits with the technicians before all systems meet expectations.
While no one likes to contemplate an electronics-refit project gone awry, following these steps means most owners can look forward to years of safer and better cruising.
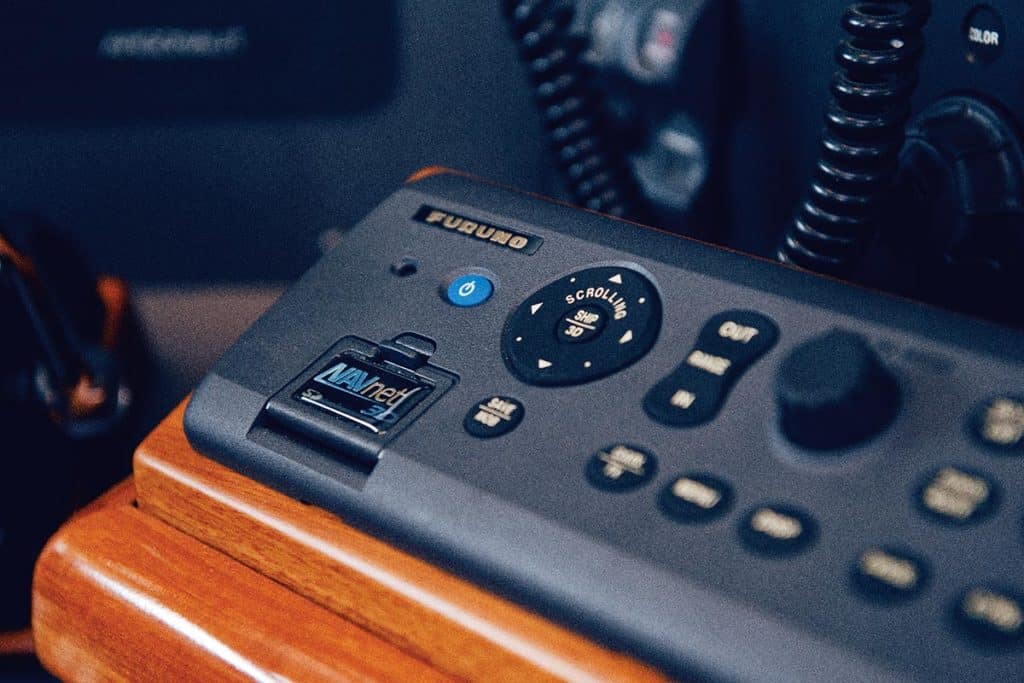