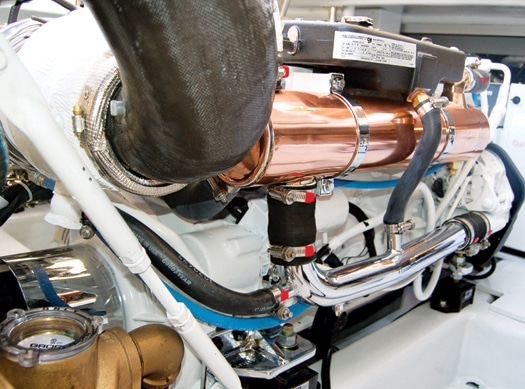
ytgjul17cool525.jpg
You’re finally headed out on that long-awaited cruise, but two hours into the trip, one of your engine’s temperature gauges is well above normal, and creeping higher.
“You finally get to use your boat, and all of a sudden it’s overheating,” says John Wheatley, owner of Florida Marine Tech in West Palm Beach, Florida. He and I have both seen it play out countless times before-Wheatley in the emergency service calls he anticipates every summer and me as a freelance captain trying to nurse an overheating boat through a Bahamas cruise. “It’s a lot simpler to provide adequate service,” Wheatley says. “The cooling systems on today’s engines aren’t marginal, like they often were in the ’70s and ’80s. If you’re servicing them every two years, you can rest assured they’re going to run cool and you’re going to have a good trip.”
Most marine diesel engines cool themselves by circulating antifreeze through the engine and then circulating seawater through a heat exchanger, which cools the antifreeze. Proper service boils down to four things: Clean and test the seawater side of heat exchangers and auxiliary coolers every two years, flush and renew the antifreeze, replace rubber seawater pump impellers and inspect systems every year, and make a few simple checks before leaving the dock in the morning. Anything less is gambling both valuable time and your engines.
Even if engines aren’t used much, cooling systems still need regular service. “You might not see barnacles, but the scale builds up and [the cooling system] won’t transfer heat,” Wheatley says. “It’s probably worse when the boat sits. You wouldn’t let the paint on the bottom go more than two years. It’s the same seawater.” Heat exchanger cores are acid-cleaned and pressure-tested, and reinstalled with new O-rings and gaskets, all greased and sealed. Postponing service often leads to corroded components and seized bolts, so saving money by waiting may cost more in the end. “Even if you just pull them apart and replace O-rings, at least you’ll see corrosion before it ruins something,” Wheatley says.
Charlie Schloemer, President of Palm Beach Power in West Palm Beach (www.palmbeachpower.com) also services many neglected cooling systems when boats hit warmer southern waters. “Someone needs to touch and feel these parts internally to see if there is any corrosion,” Schloemer says. “Engine hours are important, but systems break down more from sitting than use.” Schloemer also warns against ignoring ancillary equipment coolers that share engines’ raw water circuits. “Return fuel coolers, marine gear coolers, steering-pump and stabilizer coolers-these are often in line between the sea strainer and engine seawater pump. Debris in the inlet side of these coolers can restrict seawater flow through the entire engine.” Cleaning and pressure-testing these pass-through coolers also ensure they won’t leak seawater into fuel or oil, damaging expensive components.
Both Schloemer and Wheatley see different maintenance issues among the various engine manufacturers, and even between models. For example, Schloemer says charge air coolers on most MTU engines are cooled by the antifreeze portion of the cooling system, so they can often go beyond two-year service intervals. But Series 60 engines cool with seawater and need close attention. Wheatley points out that Cummins diesel aftercoolers are more sensitive to corrosion from delayed service than other components, while on MAN engines, heat exchangers are most prone to trouble.
Antifreeze breaks down over time, too. A chemical flush removes sediment and scale, and fresh antifreeze protects the system from corrosion. Boats that winter in colder climates require a 50-percent ratio of antifreeze to water, but in southern waters, using only 30 percent antifreeze may result in cooler-running engines since water moves more heat than antifreeze does. Consult engine manufacturers’ guidelines for coolant to avoid harming engine-specific alloys and components, and check coolant with test strips or a simple automotive hydrometer every few months.
Some engine seawater pumps have bronze impellers, instead of traditional flexible rubber impellers. With either type, inspect the underside of the pump with a mirror or by feel. A leaky pump will be wet or have mineral deposits at the telltale hole at the bottom of the cavity that separates pump seawater seals and engine oil seals. An occasional drip at cruising rpm should be watched but doesn’t necessitate immediate attention, but over time leaks can erode the stainless steel shaft all the way through the oil seal, letting seawater into the engine oil. Schloemer suggests rebuilding pumps entirely every two years.
Engines’ antifreeze circulating pumps are similar to bronze seawater pumps, but since they operate only in antifreeze, they typically last until engines are overhauled. Inspect them, though, for telltale pink or green antifreeze stains on the underside that show they’re beginning to leak.
Schloemer emphasizes checking coolant levels before each trip. “You could lose three or four gallons of coolant and not know it. If you have an internal leak, when you go to crank it the next day, you might bend a rod and not know that. Eventually [the rod] will break and might go right through the block,” he says. “If an engine seems to bog down when starting, don’t assume it is the batteries.” Schloemer also warns not to trust those easy-to-see plastic coolant expansion bottles blindly, as a pinhole in the hose connecting it to the heat exchanger, or a defective heat-exchanger cap may prevent coolant from siphoning out of the bottle. “When the engine is hot, the coolant will be higher. When it is cold, it should be lower.” He says this cycling indicates a properly working overflow bottle. If in doubt, check the heat exchanger directly. “Normally [the antifreeze level] should be within three inches of the top. On a cold engine, you should be able to touch it with your finger,” he says.
If the coolant level is low, look for the cause. An external leak will likely evaporate in the heat of the engineroom, but the odor of antifreeze in the engineroom is a sure sign. “It’s a sweet smell, or sometimes a bitter, rank smell,” says Schloemer. “Sniff the clean antifreeze in a jug. It is a very distinct odor.” Minor external leaks won’t ruin a trip, but monitor them closely until repaired. An odor of antifreeze or noticeable white smoke (actually steam) in an engine’s exhaust indicates a more serious internal leak that must be addressed immediately.
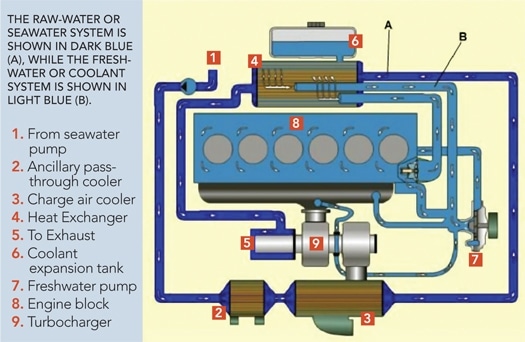
| | |
The generator shares the same issues as the engines, but the genset’s power-generating equipment also needs to stay cool. “Generator engines use water to cool themselves, but most [electrical] components use airflow,” says Mark Turpin, a mechanical engineer with Cummins Power Generation. (www.cumminsonan.com) “They’re designed to last 20,000 hours or more, but if the alternator runs hot enough, that could reduce to 5,000, 100, or even two hours.” Generators cool themselves with adequate air, but Turpin says neglected ventilation systems are common, particularly when generators are located outside of the main engineroom. Blocked sound-enclosure vents are another. “I’ve seen boxes stacked against the inlet ducts, or loose equipment that falls and blocks the airflow,” he says. Loose sound-deadening insulation can disrupt airflow inside generator sound enclosures or block air-intake vents. Sound-enclosure air dams, which separate cool incoming air from hot air discharged through the alternator, should be checked as well.
The best way to ensure your engine is cooling itself properly is to check it periodically at full throttle. If an engine won’t reach rated rpm, don’t push it. Instead find out why right away. If it will reach the rated rpm, hold it at the maximum for three to five minutes. If temperature gauges creep too high, they’re warning you that it won’t be long before engines overheat at cruising rpm, too.