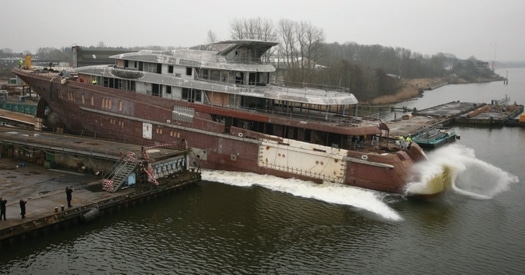
ytgmay09perf525.jpg
Over my many years of designing them, I’ve often been asked, “What’s the best material for building yachts?” It’s a simple question that is heavily debated.
Wood used to be the easy answer. Whether clinker or carvel planked, yacht construction was all wood. The first example of anything else that I know of can be found in the 1897 edition of Dixon Kemp’s classic text Yacht Architecture. In a chapter entitled “Composite Construction” there are examples of wood planks on iron frames. Of course, composite construction today means something entirely different.
In the 100 years it took for composite construction to change meanings, we added steel, aluminum, various plastics, and even ferrocement to the material list. And now each material is available in a variety of forms. As a result, many yachts employ several materials, and you can see the possibilities are endless.
As new materials were introduced, many of them in the post-war boom of the late 1940s and early 1950s, boatbuilding pioneers ventured into the wilderness. Early wisdom was that steel was most suitable for large yachts and fiberglass appropriate only for small boats, but there were challengers. Hatteras built big yachts in fiberglass and Steelcraft tried smaller steel boats. Surviving better in the fresh water of the Great Lakes than in salt water, many Steelcraft yachts succumbed to corrosion and the company finally ceased production. Hatteras Yachts did considerably better, becoming the industry leader in the 1960s.
The lesson is that proper material selection, whether you’re building one yacht or thousands, is critical to success. Among the many factors to consider, perhaps the most important are weight, strength and corrosion resistance. Secondary to these are the size and shape of the hull, the intended use of the craft, and cruising grounds. For diehard brand loyalists, your builder may not offer construction in what would otherwise be the preferred material, so a compromise might be required.
Finally, there are differences in material and labor costs, although in the end, these are not often substantial for a fully equipped and finished yacht.
In the 50- to 100-foot range-common materials can be used with success-the exceptions being rotomolded plastic, suitable only for small boats, and ferrocement.
Wood can be worked as solid planks or plywood. Today, many yachts are cold-molded using wood strips and resin. Wood offers thermal, acoustic, and aesthetic advantages that other materials, particularly metals, find tough to match. Saturating the wood in resin reduces maintenance issues, but does not eliminate them.
Aluminum, which is costlier than steel, is very light for its strength. Proper selection of marine alloys is essential; other grades will not stand up in a salt environment. For yacht-grade finishes, application of fairing compound is usually required, and the material is susceptible to corrosion if proper precautions are not taken.
Steel is strong, even in light gauges, and can be repaired at even the most rudimentary facilities. It is amenable to both cold and hot climates, allowing it to be shaped into compound curves and complicated shapes. Susceptibility to rust is a distinct disadvantage. This can be minimized with careful attention to design, construction details, and the proper application of modern coatings.
Composites are perhaps better suited to production yachts than custom ones, although several builders specializing in one-off construction deliver a superb job. Advantages include the ability to mix and match a plethora of resin and reinforcement choices to meet strength, weight, and dimensional requirements. Corrosion concerns are generally nil, but there are special concerns with electrically conductive carbon graphite reinforcements that should not be ignored.
Each of these materials has pros and cons, so it is not surprising to see designers pick and choose to create the ideal custom yachts from a mix of materials. A common palette is mild steel for the hull, polished stainless steel for stanchions and rubrails, aluminum for the superstructure, composites for the radar arch and window frames, and of course, the unmatched warmth of wood for handrails and joinery.